.
Ganadores Advanced Manufacturing Awards 2024
Best Design Innovation and Product Development
EURECAT, Púlsar
Descripción y objetivo del producto o proyecto
El objetivo de llevar a cabo este producto se basa en poder demostrar el potencial de la tecnología de In Mold Electronics también conocida como Plastrónica para poder demostrar físicamente el potencial de esta tecnología para cualquier superficie plástica susceptible de integrar tecnología para convertirla en una superficie funcional e inteligente. Como objetivo poder demostrar los beneficios de la tecnología a potenciales clientes. Algunas de sus ventajas son:
Reducción de la complejidad en los productos fabricados en plástico (menor número de piezas).
Automatización de los procesos de acoplamiento. Fabricación monolítica simplificada a una sola pieza, sin montaje en producción.
Integración de electrónica en geometrías complejas y piezas en contornos 3D.
Reducción de espesores (hasta el 80%).
Reducción del peso de la pieza (hasta el 60% más ligera que con el PCB tradicional).
Aumento de la funcionalidad de la pieza.
Mayor durabilidad de la electrónica, dado que se encuentra encapsulada/protegida.
Incremento de la libertad en el diseño de nuevas formas y capacidades en las piezas.
Imagen 1 (JPEG, JPG, PNG, GIF)
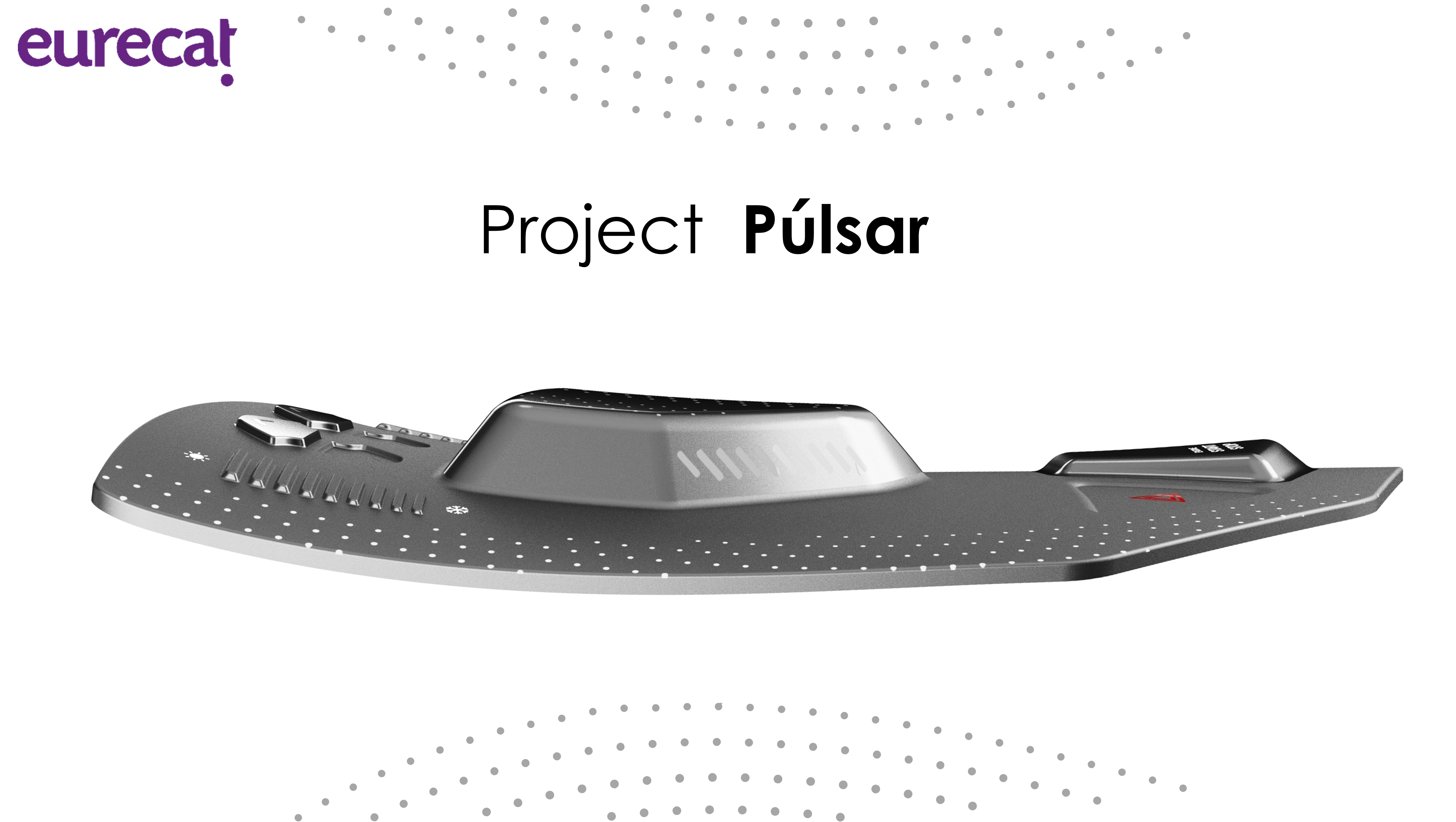
show more
show less
Best Technology Disrupting the Production Process
Industrias Alegre S.A., Innovación en proceso de fabricación para módulos de baterías
Descripción y objetivo de la tecnología utilizada en el proceso de producción
La tecnología principal utilizada en este proceso de producción es el moldeo por inyección con sobreinyección de insertos metálicos en una maquina vertical, en combinación con soldadura por ultrasonidos y control de calidad con cámaras de visión.
En el moldeo por inyección vertical, la unidad de cierre está en posición vertical, esto supone que el molde se despliega en dirección vertical. Siendo así, hay una mitad de molde superior y una mitad inferior. La inyectora introduce el plástico a través de la mitad superior del molde. Después de la inyección la prensa abre, subiendo la mitad superior del molde y dejando libre la mitad inferior que se desplaza fuera de la maquina con las piezas ya acabadas.
En nuestro caso hemos aplicado el concepto de maquina vertical a una prensa de gran tonelaje (1700T), que no es nada habitual en prensas verticales. Para conseguir altas producciones en este proyecto, la maquina es especial y se ha diseñado con dos mesas deslizantes, una a cada lado de la máquina. De esta forma tenemos dos partes inferiores del molde, una en cada mesa, de forma que siempre hay una de ellas inyectando mientras que en la otra se están extrayendo las piezas acabadas y colocando los insertos para el siguiente ciclo.
En cada pieza de plástico se sobreinyectan 17 insertos metálicos, la mayoría de ellos son los busbars de aluminio. Estos tienen que quedar perfectamente limpios de plástico por el lado donde se hacen las conexiones de las pilas en el módulo. Y para asegurar que queden perfectamente asentados en el molde y sin filtraciones de plástico por detrás, en el molde tenemos unos pines de sujeción para que no se muevan durante la inyección.
Esos pines de sujeción dejan agujeros en el lado de las piezas donde se colocan las baterías, y esto podría generar un riesgo de arco eléctrico por el hecho de que los aluminios estén al aire en el lado de las baterías.
Por eso tenemos que hacer un proceso de soldadura posterior a la inyección. Se trata de soldadura por ultrasonidos para derretir el plástico alrededor de cada agujero y conseguir que quede tapado. Soldamos 90 puntos por pieza en una maquina rotativa con 3 mesas que giran para que el proceso se vaya completando con un ciclo capaz. El proceso de soldadura se realiza justo a continuación de la inyección.
Hay varios puntos en el proceso en los que hacemos controles con visión, para asegurar la calidad de las piezas y mínimo scrap:
1. Cuando los operarios colocan los insertos de aluminio en unas cunas para preparar todo para el robot.
2. Después de que el robot coja los insertos y los deje en su posición correcta en el molde.
3. Tras la inyección, una cámara de visión chequea que no hay ninguna filtración de plástico por debajo de los aluminios.
4. Tras cortar las entradas de material.
5. Por último, en la estación de soldadura, que comprueban que los 90 puntos están soldados correctamente.
Imagen 1 (JPEG, JPG, PNG, GIF)
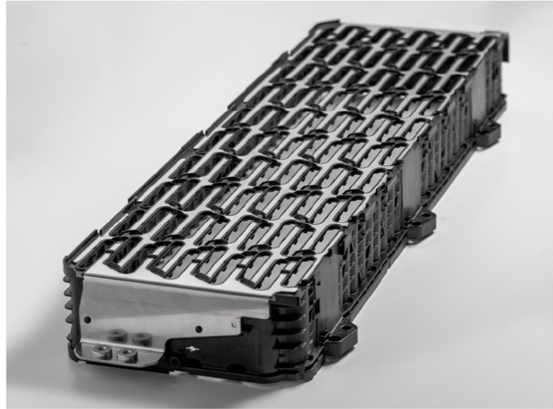
show more
show less
Best Innovative Technology in Composites Manufacturing
Aldakin, Sistema robótico para el mecanizado seguro y preciso de materiales compuestos
Descripción y objetivo de la tecnología utilizada en el proceso de producción
Con el objetivo de mejorar la salud y la precisión en el mecanizado robotizado de composites, se ha desarrollado un sistema robotizado que incluye un sistema interno de aspiración de polvo que mejora las condiciones de salud y seguridad de las personas al minimizar la exposición al polvo con fibras y resinas. Además, la solución genera un menor consumo de energía, un mayor rendimiento (3 veces más preciso que los robots actuales) y consta de control continuo para un mecanizado "cero” defectos.
Imagen 1 (JPEG, JPG, PNG, GIF)
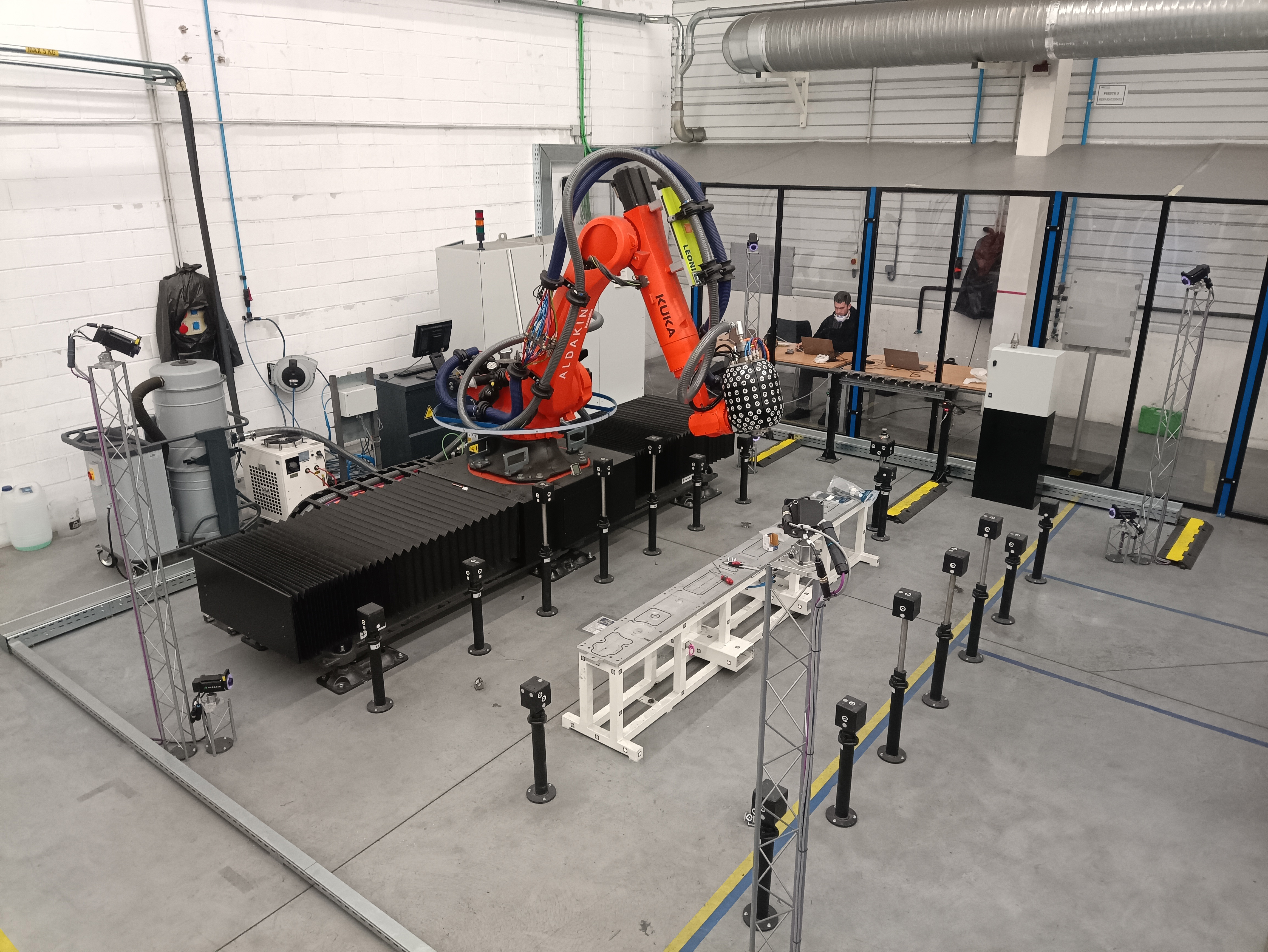
show more
show less
Best Automation and Robotic Integration
CIFP ESCUELA HOSTELERÍA LEIOA LHII, Robótica en la gastronomía
Descripción y objetivo del proyecto de automatización o robótica
El proyecto de robótica de robótica de cocinado de paella es una iniciativa innovadora que emplea robots colaborativos (cobots) avanzados para automatizar y optimizar la preparación de este icónico plato español. Desarrollado en nuestra escuela de formación profesional de hostelería, el sistema está diseñado para mejorar la eficiencia y consistencia en la cocina, reduciendo el desperdicio de alimentos y los costos operativos.
Objetivos del proyecto:
* Mejorar la eficiencia operativa: Los cobots automatizan tareas repetitivas y precisas, permitiendo una preparación rápida y consistente de la paella, incrementando la capacidad de producción en un 40% y reduciendo errores en un 25%.
* Garantizar la calidad y seguridad alimentaria: La automatización minimiza la contaminación cruzada y los errores humanos, asegurando que cada paella se prepare con los más altos estándares de calidad y seguridad.
* Fomentar la sostenibilidad: El sistema utiliza ingredientes de manera precisa, reduciendo el desperdicio alimentario y optimizando el consumo de energía, lo que contribuye a un entorno más sostenible.
* Capacitar a futuras generaciones: Integrar tecnología avanzada en la formación de nuestros estudiantes prepara a futuros profesionales para enfrentar los desafíos y aprovechar las oportunidades de un mercado en evolución, promoviendo habilidades en robótica y gestión tecnológica.
* Promover la innovación en la hostelería: Al combinar la tradición culinaria con la tecnología de punta, el proyecto posiciona nuestra escuela y a sus graduados como líderes en la innovación dentro de la industria gastronómica.
Imagen 1 (JPEG, JPG, PNG, GIF)
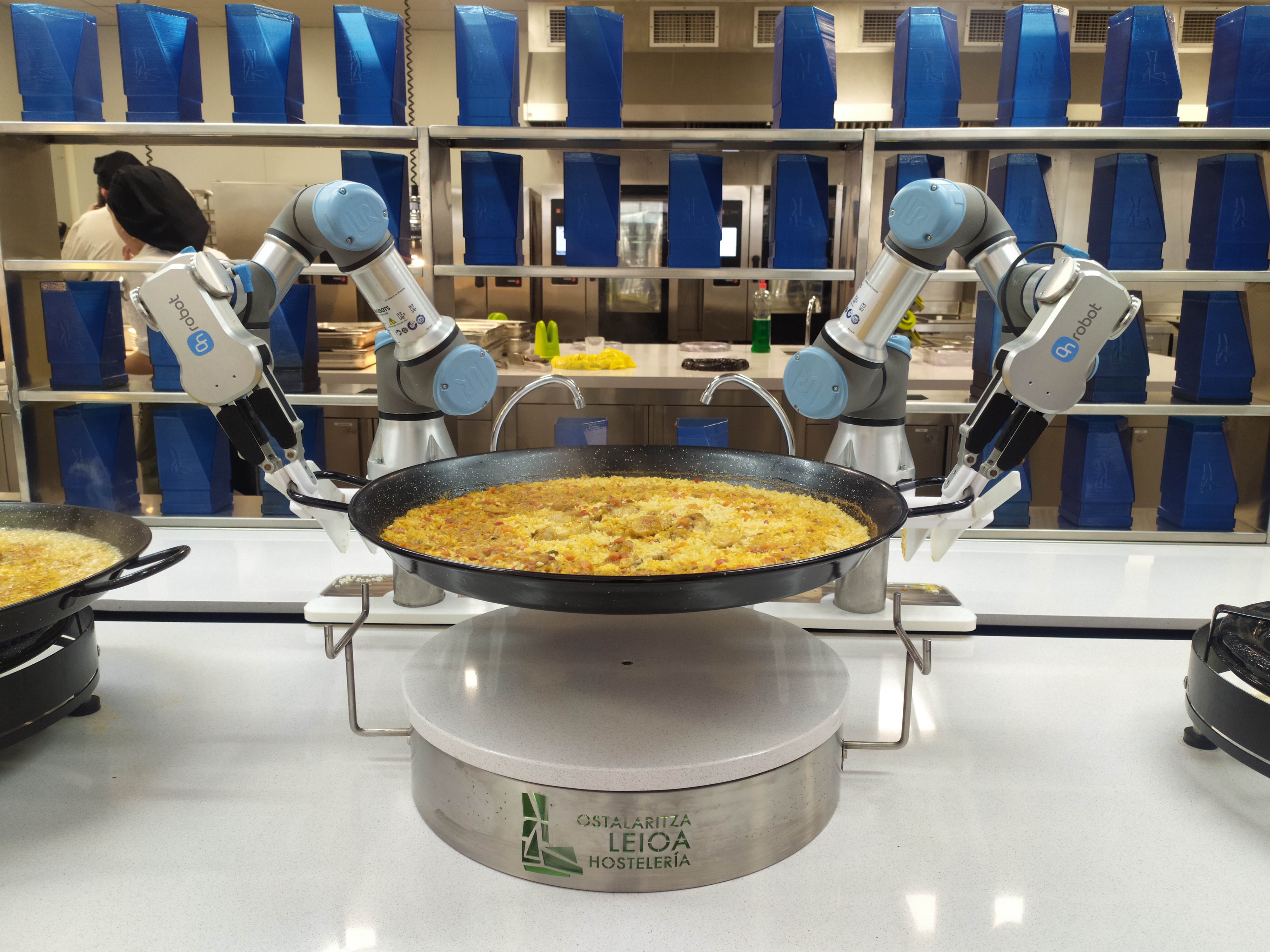
show more
show less
Best Product Testing and Quality Assurance
MESbook, GAZC: APQP Digital aplicado al sector del mecanizado
Descripción y objetivo de la prueba de producto o control de calidad
Sea cual sea el proceso que debemos gestionar, ya sea estampación en frío con prensa progresiva o transfer, decoletaje, plegado, punzonado, mecanizado, montaje, soldadura, corte láser, etc., siempre deberemos tener control de los puntos de relevancia de nuestro proceso.
MESbook permite asegurar que se trabaja tal y como se ha definido previamente (eficacia), ayudando a las personas a:
• Evitar errores y olvidos
• Asegurar que se trabaja conforme al último nivel de diseño de procesos.
• Realizar los set-ups adecuados de las máquinas.
• Facilitar que todas las personas trabajen sincronizadas.
• Aprovechar al máximo los RRHH y las máquinas.
• Reducir inventario.
• Conseguir que el conocimiento sea propiedad de la empresa y no solo de los trabajadores.
El APQP Digital completamente implantado en GAZC y desarrollado por MESbook es una solución única e innovadora que transforma el enfoque tradicional de las Core Tools de APQP actualmente utilizadas en la industria manufacturera mediante su integración total con la realidad de la fábrica, iniciativa destinada a redefinir los estándares de calidad en la industria.
Esta integración incluye máquinas, procesos, sistemas y personas, proporcionando beneficios inigualables en la reducción de costes indirectos al consolidar todas las herramientas en una única plataforma de gestión de fábrica conectada en tiempo real.
Su principal objetivo es garantizar la calidad del producto desde la fase de diseño hasta la producción en serie mediante la integración de herramientas avanzadas de gestión y análisis en tiempo real. El sistema abarca desde el Análisis de los Modos de Fallas y sus Efectos de Diseño (DFMEA) hasta la Validación de Producto y Proceso, ofreciendo un enfoque estructurado y sistemático para minimizar riesgos y optimizar la calidad en cada etapa del ciclo de vida del producto. La implementación del APQP Digital permite a las empresas lograr productos y procesos robustos, reducir costes y asegurar el cumplimiento de los requisitos normativos, como IATF 16949 e ISO 9100, de manera completamente digital.
Al diseñar un producto y su proceso de fabricación, normalmente requiere de la involucración de muchos departamentos, máquinas e incluso empresas cuando parte del sistema se fabrica en los proveedores.
Para ello, es imprescindible poder gestionar todos los pasos que aseguren que cada parte individual cumplirá con los requerimientos de producto, proceso, calidad, coste y plazo de una manera robusta.
Normalmente, las empresas realizan esta labor apoyándose en documentos, hojas de cálculo, bases de datos, reuniones, correos electrónicos, etc.
La propuesta de MESbook consistió en poner a disposición de GAZC una plataforma digital que permita la gestión integral de los proyectos de lanzamiento de nuevos productos o modificaciones de los existentes, dando cobertura a todos los hitos funcionales de un nuevo diseño.
Imagen 1 (JPEG, JPG, PNG, GIF)
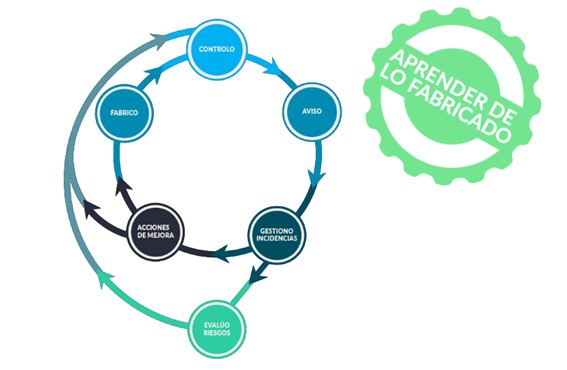
show more
show less
Smart factory: best connected production chain
T702 Visual SLAM y AMR Studio, ASEA BROWN BOVERI, SA
Descripción y objetivo del proyecto de cadena de producción inteligente
El AMR Flexley Tug T702 lleva incorporado la tecnología de navegación Visual SLAM basada en inteligencia artificial y dispone del avanzado software AMR Studio®. Este robot mejora la flexibilidad y la productividad en la cadena de producción y su sistema es mucho más conectado e inteligente que los robots móviles automatizados convencionales equipados con escáneres 2D SLAM. Además, es capaz de reconocer el entorno dinámico y navegar por él de una manera mucho más eficiente: detectando objetos fijos y móviles, así como personas. El nuevo software AMR Studio® permite el control de los AMRs desde un único sistema sin necesidad de múltiples programas. El software combinado con la tecnología Visual SLAM es muy fácil de usar y de instalar, y solo hay un sistema AMR, por lo que se optimiza el tiempo de puesta en marcha en un entorno de producción hasta en un 20%. El sistema gestiona la misión y las órdenes en los AMR y permite monitorizar toda la flota de AMR en todo momento. De esta forma, se controla y mejora la productividad de toda la cadena y se localizan los posibles errores para que puedan ser resueltos rápidamente. En definitiva, se consigue robustez, precisión y máxima flexibilidad, lo que conlleva un aumento de la productividad y la eficiencia, un mayor retorno de la inversión y una mayor seguridad.
El objetivo es dotar a industrias como la logística, la intralogística, la automoción o los bienes de consumo de una gran flexibilidad y escalabilidad, especialmente en grandes almacenes y centros de distribución donde el entorno puede estar en constante cambio, mejorando su cadena de producción para que cuente con inteligencia que les permita ser más eficaces. Otro de los objetivos de este proyecto es permitir a los usuarios con poca experiencia en programación operar y programar fácilmente flotas de robots móviles.
Imagen 1 (JPEG, JPG, PNG, GIF)
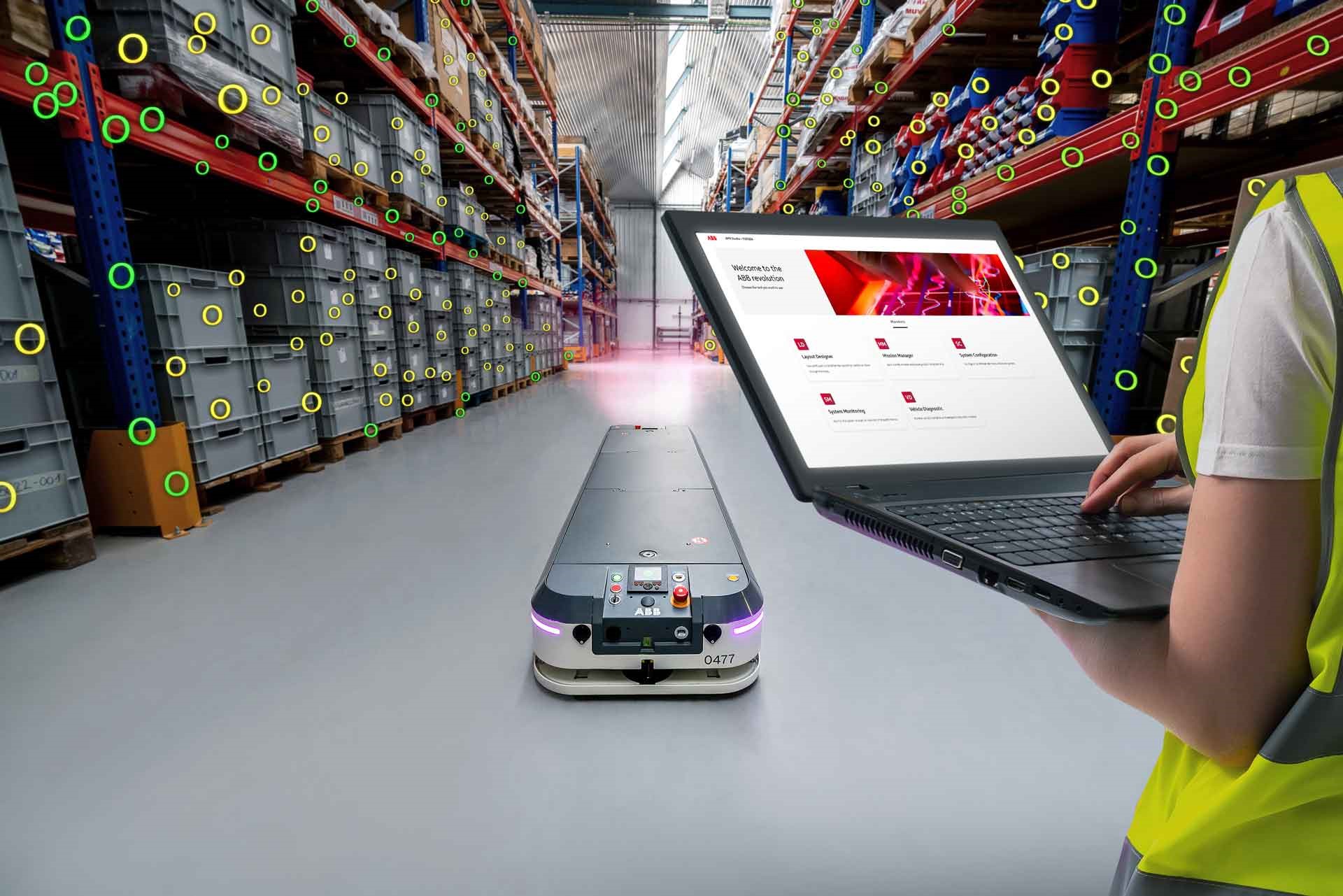
show more
show less
Best Sustainable & Circular Economy Project
HRE HIDRAULIC S.L, BECOLD
Descripción y objetivo del proyecto sostenible
El proyecto BeCold, desarrollado por HRE en colaboración con Tecnalia y UPV/EHU, tiene como objetivo eliminar total o parcialmente el uso de taladrinas y aceites de corte en los procesos de mecanizado, reemplazándolos con un sistema de lubricación y refrigeración basado en gas criogénico CO₂. Este cambio busca reducir el impacto ambiental, los costos operativos y mejorar la salud laboral al minimizar la exposición a productos químicos nocivos. Tradicionalmente, las taladrinas y aceites de corte se utilizan ampliamente en el mecanizado debido a su capacidad para reducir el calor y la fricción, pero su uso conlleva desventajas significativas, como altos costos, generación de residuos peligrosos y riesgos para la salud de los trabajadores.
BeCold se presenta como una solución innovadora y sostenible, ya que utiliza CO₂ reciclado de procesos industriales y aceites para microlubricación (MQL) de base vegetal. Este enfoque no solo reduce el consumo de lubricantes y energía eléctrica, sino que también mejora la productividad y calidad del proceso de mecanizado. La tecnología de refrigeración criogénica permite mantener las herramientas de corte a bajas temperaturas, reduciendo el desgaste y extendiendo su vida útil, lo que a su vez disminuye la necesidad de reemplazos frecuentes y la generación de residuos.
El desarrollo del proyecto comenzó en 2014 y ha avanzado significativamente desde 2019, con la industrialización del producto y pruebas beta en las instalaciones de UPV y TECNALIA. Estas pruebas demostraron la eficacia de BeCold en la reducción de costos y tiempos de mecanizado, así como en la mejora de la calidad de las piezas terminadas. Además, el sistema es fácil de integrar en las máquinas-herramienta existentes gracias a su diseño "plug and play", lo que facilita su adopción en diversas industrias. Es por ello, que desde el 2022 ya estamos vendiendo en clientes.
En términos de impacto ambiental, BeCold contribuye a la economía circular al reutilizar CO₂ y reducir la necesidad de aceites minerales, que son difíciles de reciclar y eliminar. La implementación de este sistema también mejora el ambiente laboral, al eliminar la exposición a productos químicos nocivos, lo que puede reducir los problemas de salud relacionados con la piel y el sistema respiratorio. Este enfoque alineado con el concepto de "Green Manufacturing" posiciona a BeCold como una solución avanzada y respetuosa con el medio ambiente, promoviendo prácticas de manufactura sostenibles.
En resumen, BeCold representa una iniciativa innovadora que aborda los desafíos del mecanizado tradicional con un enfoque en la sostenibilidad y la eficiencia. Su objetivo principal es transformar los procesos industriales hacia un modelo más ecológico, reduciendo costos, mejorando la productividad y minimizando el impacto ambiental. Con el respaldo de instituciones tecnológicas y una sólida base de investigación y desarrollo, BeCold está preparado para hacer una contribución significativa a la industria del mecanizado y avanzar hacia un futuro más sostenible.
Imagen 1 (JPEG, JPG, PNG, GIF)
catalogoBecold A4 es.pdf
show more
show less